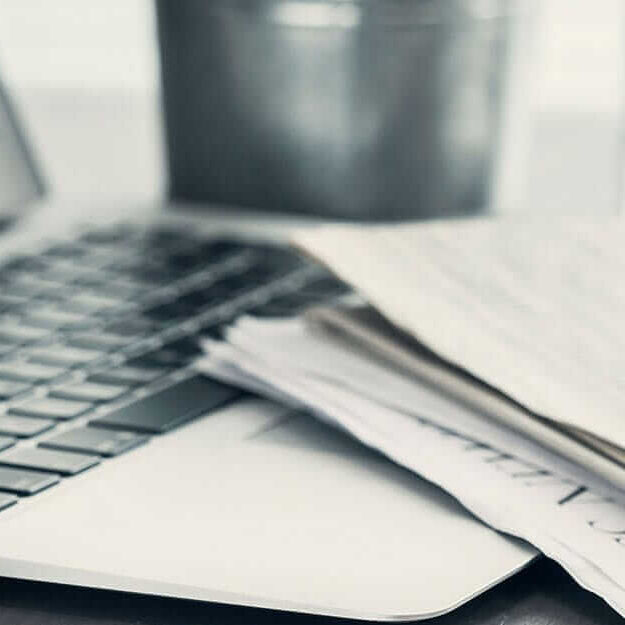
Newsroom
A. O. Smith Corporation is one of the world's leading manufacturers of residential and commercial water heaters. Browse our latest news, case studies and more.
A. O. Smith Corporation is one of the world's leading manufacturers of residential and commercial water heaters. Browse our latest news, case studies and more.